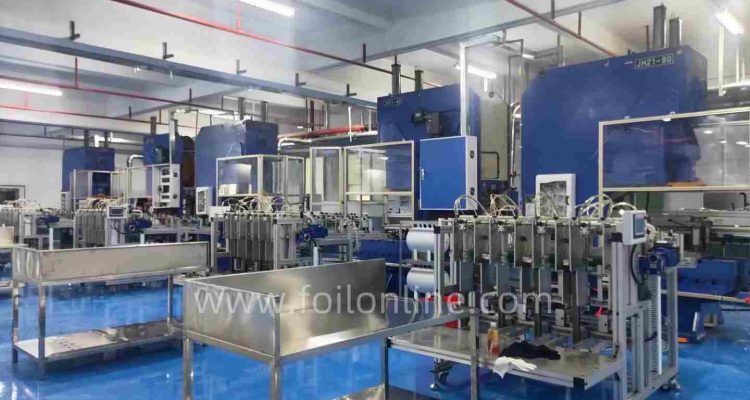
How Advanced Automation in Foil Container-Making Machines Reduces Production Costs
Introduction
In today’s fast-paced world, aluminum foil containers have become essential in the packaging of food items among ready-to-eat meal providers. Due to these growing demands, producers have been looking to make production lines faster and more efficient yet more economical and with less cost. What’s one of the best solutions? Advanced automation in foil container-making machines.
Automation technologies allow machines to repeat operations with minimal human interaction intervention. Automation saves time and money by keeping the quality consistent. Present-day machines can produce many more containers in less time with fewer errors due to programmable logic controllers and automatically controlled quality control systems. For this reason, the machine is ideal for companies that need to meet high production demand without increasing labor costs.
Automation of the highest level in the machines that prepare the foil containers currently changes the face of the industry through cost reduction, qualitative improvement, and efficiency in manufacturing. From upgrading machines to learning about industry trends, this will be a highly valued guide.
Let’s dive into a world of automation and cost-saving innovations!
What is Advanced Automation in Foil Container-Making Machines?
Advanced automation of foil container-making machines means using technology to speed up production processes and make them more precise and efficient. Programmable Logic Controllers are at the core of such automation. Working as a “brain” within the machine, the PLC controls everything from the speed and pressure to timing specifics so that each container is precisely reproduced as needed.
With PLCs, manufacturers could finally let their machinery operate with little interference from human operators, enabling them to minimize errors and maintain high production rates.
The last key constituent of advanced automation involves a quality control system. In the latest machinery, sensors and cameras are employed to inspect containers that may have cracked or uneven edges automatically. It helps the manufacturer catch mistakes earlier, with less waste and higher quality. These quality control systems eliminate time-consuming manual inspections, allowing each container to meet set standards.
Another important element in the machinery is the automated feeding systems. These systems automatically feed the rolls of aluminum foil into the machine, thereby reducing the time spent loading materials. It also reduces waste to the minimum by using accurate measurements that are necessary for cutting foil. It saves not just material but reduces overall cost in general.
Combined, these sophisticated technologies accelerate, flatten, and economize the manufacturing of foil containers. They enable manufacturers to respond to high demand without additional investment and compromising quality, making automation a worthy investment in foil containers.
How Automation Reduces Production Costs in Foil Container Manufacturing
Labor Cost Reduction
Labor costs are one of the major cost-saving advantages of automated foil container-making machines. The automated machine performs nearly everything, from feeding to shaping, edge trimming, and stacking finished containers. Such setups reduce any need for human intervention to the minimum possible.
Thus, a manufacturer can save on labor costs without compromising productivity. Because only a few employees are now required to perform these tasks, companies can reduce overhead significantly while keeping production rates high.
Material Efficiency and Waste Reduction
Automation also leads to material efficiency, which is the reduction in waste generated. The traditional methods of manufacture result in wasted materials, probably because they are less keen on cutting the foil to exact measurements.
On the other hand, automatic machines use accurate measures to cut just enough aluminum foil for a particular container. It minimizes scraps and, over time, cuts down on raw material costs, enabling the manufacturer to save money while making the line of production more viable by maximizing the use of every foil roll .
Reduced Downtime and Lower Maintenance Costs
Advanced automation cuts downtime and reduces maintenance costs. An automated system is designed to operate day and night with as little downtime as possible.
Many machines have predictive maintenance features that alert operators to potential problems before they become breakdowns, saving the manufacturer from expensive repairs and surprise delays in production. Smaller numbers of disruptions imply smoother production lines and the capability to meet high demand with no additional costs from delays.
Faster Production Cycles and Energy Savings
Automated machines work much faster and smoother, enabling manufacturers to increase production speed without necessarily adding shifts or working overtime. With a capacity to produce hundreds or thousands each day, an automated system will meet the demands of the market a lot faster. This speed cuts down labor and energy costs, hence increasing its efficiency and profitability in general.
Efficiency and Quality Benefits of Advanced Automated Machines
Increased Production Speed
One of the major advantages with regard to automated machines is that they speed up production to a whole new level. In contrast, they could produce hundreds, if not thousands, of containers in one day as opposed to manual means.
It will enable companies to supply products in high demand within a short time without necessarily increasing more shifts or extra labor. High speeds cut down delays experienced during the fulfillment of orders, improving customer satisfaction and the growth of business in general.
Automated Quality Control
Apart from production, quality control is another area that benefits from quality assurance in these machines. Automatic machines scan each container in production and can be checked for defects like flaws, uneven edges, or wrong shapes. They are equipped with cameras and sensors of high resolution.
Based on the mechanism designed by the engineers, machines automatically remove such containers to raise their quality and make them customer-worthy. By this quality mechanism, the need for hand inspections decreases, which further cuts down on time and encourages cost reductions.
Versatility and Flexibility in Production
In Production, Automated machinery provides great flexibility and versatility. Most systems allow for rapid changes in settings, allowing manufacturers to switch from container sizes or designs to others without necessarily stopping production. Such adaptability features are quite important to companies that offer a wide range of containers because they can meet various customers’ demands without wasting time on setting changes.
Whether a company requires small single-use trays or larger bulk containers, an automated machine can easily adapt to the size with consistency and efficiency.
These improvements in efficiency and quality combined meet the high demands of production while ensuring the consistency needed today in such a competitive foil container industry, done largely by automated machines.
Assessing ROI for Automated Foil Container-Making Machines
The investment in premium Automatic Foil Container-making Machines has their return on investment looked at for long-term value. The higher cost of a machine often offsets any upfront savings, making worthwhile investments in those. Companies save by reducing labor costs, minimizing waste, and creating a more efficient production environment, so the return on investment could be realized within a few years.
While calculating the returns, these companies should keep in mind a number of factors: one, the big labor savings are on account of lesser human intervention because these machines themselves take up the jobs of feeding, trimming, and stacking; second, material savings due to precise cuttings reduces the wastage of raw material, saving raw aluminum foil costs.
These savings combined usually mean an automated machine gives a higher return over time than traditional equipment. Besides, with automated machines, the production capacity increases the way for taking large-size orders, thus helping a business grow without increasing its labor force. The added efficiency in production further increases the ROI by reducing the per-unit cost of each container produced.
However, with a decrease in labor and material costs and an increase in output, the justification for using automated foil container-making machines to improve profitability within the packaging industry is very strong.
Future Trends in Automation That Could Impact Foil Container Manufacturing
With several upcoming trends boosting efficiency and cost savings, the future is bright for automation in the manufacturing process of foil containers. Some of the trends that are looking good are IoT and AI integration.
IoT sensors would offer real-time machine performance monitoring, enabling the manufacturers to find out early when there is a problem and reduce downtime. AI-driven data analysis can pinpoint fine adjustments to optimize production settings in a way that further reduces waste and improves efficiency.
Another important trend involves sustainability. In the same way consumers and industries move towards greener practices, automation systems are changing. New technologies help reduce usage amounts in the amount of aluminum used per container by using thinner but more durable foil containers.
It helps in reducing material costs and minimizes production’s environmental impact. Furthermore, using recyclable aluminum and automated quality controls contributes to a much greener process and meets growing demands for green manufacturing.
Ultimately, personalization and flexibility make a difference. Considering changes in consumer preferences, it’s designed so that today’s automated machines can quickly switch the size and shape of the containers. This way, the same machine can be used for different products of the same company, immediately answering the changes in market requirements without stopping production.
With such development, the manufacturing of foil containers will continue to be in the direction of efficiency, flexibility, and sustainability while meeting industrial requirements and satisfying customers.
Conclusion
Advanced automation in foil container-making machines has much to offer for cost savings and higher speeds to manufacturers, along with quality control. They minimize labor and raw material costs and increase efficiency; hence, the machines have become indispensable in today’s competitive packaging industry. Automation also blends with trends like sustainability and personalization, enabling businesses to respond to market demands.
FoilOnline introduces top-quality, fully automated machinery for those manufacturers who want to upgrade their production. Our machines assure your business of efficient, accurate, and reliable production through advanced technologies. With automated systems that reduce waste while maximizing output in place, FoilOnline supports companies in reaching long-term savings and growth.
Welcome the future of the manufacturing of foil containers with the innovative solution provided by Foil Online. Discover how our automated machines can give a breakthrough in your production process and command competitive power in the market.
Call to Action
Ready to streamline your production and boost efficiency? Explore FoilOnline’s advanced foil container-making machines! Our machines are the ideal choice for manufacturers aiming for top-quality results. They are designed for precision and savings. Contact us today to discover how FoilOnline can elevate your production process!